General
8 Ways To Reduce Time And Cost Of Medical Equipment Production
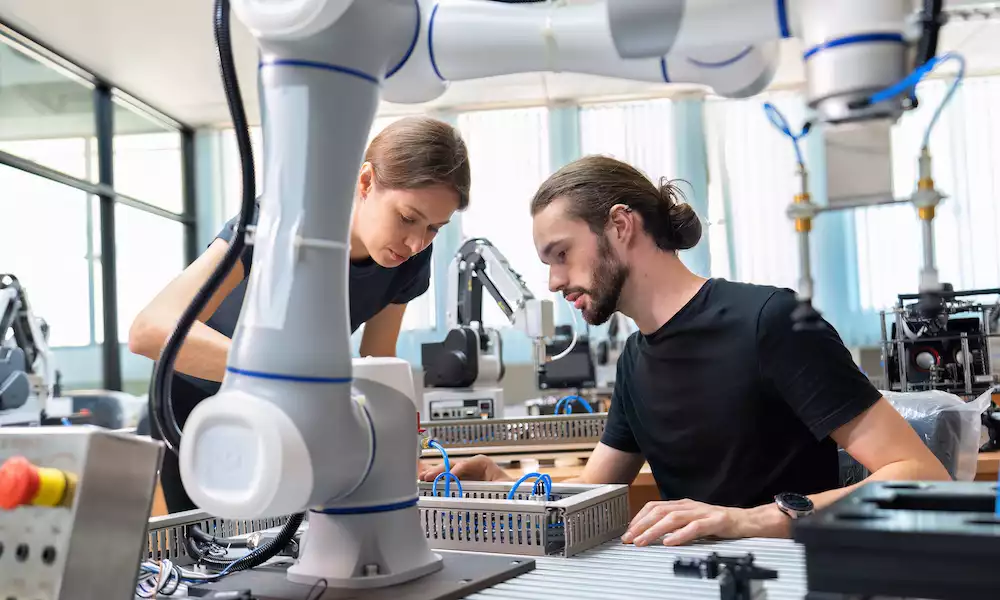
Any medical equipment should meet specific regulatory requirements before approval for usage.
As such, equipment production can be costly and time-consuming. The production process involves several steps: design, testing, and manufacturing.
Streamlining each step of the production process is vital to reduce the cost and time associated with producing medical equipment. But while you may seek to cut costs and time needed to produce the equipment, you should not sacrifice quality and compliance.
Quality assurance is critical in medical equipment production, as any substandard products can be dangerous for patients and fail to meet regulatory requirements.
Reduce Time And Cost Of Medical Equipment Production
Below is a detailed guide on reducing the time and cost of medical equipment production.
1. Use Rapid Prototyping
Rapid prototyping is a cost-effective way to test potential designs quickly. This process involves using 3D printing and other computer-aided technologies to create working models of the products.
By comparing different prototypes, you can reduce time spent on development and testing and cut costs associated with trial and error.
Through prototyping, you also create predictable results from your design. The design will be created with regulatory standards in mind before the actual manufacturing begins.
As a result, the equipment will not need to go through repeated manufacturing and testing cycles before it’s approved and released to the market.
2. Have A Strong Development Team
Having a solid team of experts to develop the product and manage the production process is essential for speeding up time to market and cutting costs. Knowledgeable personnel with pertinent knowledge about the healthcare industry and its regulations should do the design.
An experienced development team can identify potential problems in the design before they become costly problems during the manufacturing process.
Apart from developing the product design, the team should be able to handle other aspects such as budgeting, assessing risks, creating timelines, and developing strategies for quality control. Combining all these skills can result in a robust and efficient manufacturing process.
3. Reduce Material Waste
Your team can cut costs by reducing material waste during production. Using materials efficiently and minimizing the energy or resources needed for each step in the process can significantly reduce costs.
To help reduce waste, invest in machinery and technology designed for efficiency. For example, you can program machines such as 3D printers and laser cutters to produce precise designs that require minimal resources.
Your team should also use materials with a longer lifespan instead of cheaper alternatives that may need frequent replacement.
4. Work With Quality Suppliers
The components used to build medical equipment are as important as the product’s design. You must work with quality suppliers who can provide reliable and compliant parts like connectors, circuit boards, and cables.
Working with suitable suppliers will help reduce delays associated with sourcing parts, as the components will be readily available for assembly.
It is also essential to ensure that the suppliers have high-quality assurance standards and that any parts procured from them meet regulatory requirements. Working with reliable suppliers can speed up production and save costs by avoiding costly recalls due to faulty products or non-compliance.
5. Employ Automation
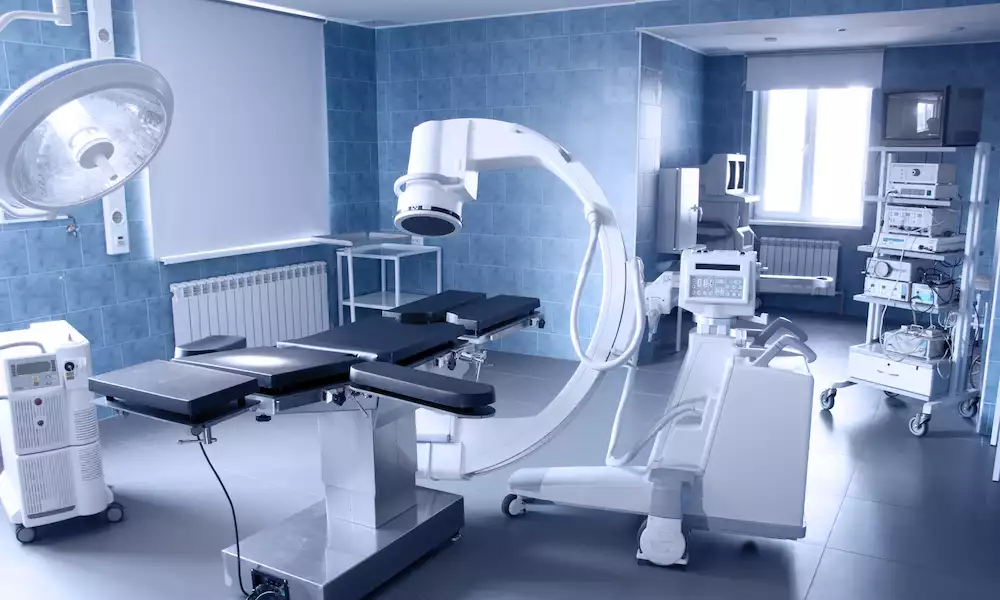
Many processes in medical equipment production are repetitive and can be automated. Automation helps reduce costs and improve efficiency by cutting down the amount of labor needed during production.
Automated solutions such as computer numerical control machines can quickly, accurately, and consistently create complex designs.
Also, automation can help ensure quality throughout the process with automatic testing and inspection systems. How? It reduces the time needed for labor-intensive quality control procedures.
Automation can also eliminate human errors that can lead to costly rework or delays during production. For example, automated systems can detect defects when printing circuit boards and adjust the process accordingly. These errors would’ve otherwise slipped into the manufacturing process if done manually, leading to delays in approvals or recalling of the products back to production.
6. Ensure Compliance With Regulations
You must ensure your products comply with the relevant regulations and standards. Several regional, federal, and international bodies guide how medical equipment is designed, manufactured, and marketed. For example, the US Food and Drug Administration (FDA) has a set of regulations for medical equipment, such as 510(k) clearance.
The FDA requires manufacturers to provide notice before introducing or reintroducing a device that has undergone significant changes that can affect its safety.
You must also ensure their medical products comply with other relevant standards, such as ISO 13485, an international quality management system standard specifically designed for medical devices.
Compliance with these regulations can reduce costs associated with recalling faulty or non-compliant products. It also speeds up the approval of the devices, allowing them to reach the market sooner.
It’s crucial to keep up with changing regulations and ensure all processes comply with the latest standards. You should have a dedicated team or personnel to manage the compliance process.
7. Get Real-Time Information About The Production Process
Investing in technologies that provide real-time production process information can quickly improve production planning, identify potential issues, and take corrective actions.
Technologies such as manufacturing execution systems give a comprehensive overview of the manufacturing process and allow for data collection from multiple sources in one place.
The information helps you make informed production decisions and prevents costly delays due to inefficient planning or unexpected issues. It is also helpful in tracking the progress of a product throughout the production line, which can help identify bottlenecks that slow down the process.
8. Ensure Quality Control
There should be quality assurance procedures to ensure all components, parts, and materials meet the required standards. They include testing for the safety, accuracy, and efficacy of the products during different stages of production.
You ought to also implement a statistical process control system besides having a development team.
The system analyzes the process and provides alerts when a significant change in quality occurs. You can then detect and trace the point of error and address any issues before they become significant problems.
Minimal errors mean faster production and less costly mistakes.
Conclusion
Medical equipment can be made faster and more cost-effective with the right processes.
Automation, compliance with regulations, real-time monitoring of the production process, and quality control are some strategies to reduce the time and costs associated with production. By implementing these strategies, you can ensure your medical equipment reaches consumers quickly and safely.